Guaranteeing Safety with Relied On Welding Inspection Milwaukee Techniques
Guaranteeing Safety with Relied On Welding Inspection Milwaukee Techniques
Blog Article
Exactly How Welding Inspection Adds To Durability and Integrity in Fabrication Tasks
Welding inspection serves as a foundational component in making sure the longevity and integrity of manufacture jobs. By systematically recognizing potential defects during different phases of manufacturing, welding inspections not only prevent expensive failings however additionally foster a society of high quality guarantee within the team.

Value of Welding Evaluation
Making sure quality via welding inspection is a vital part of any construction job. It functions as a secure to validate that welding procedures meet recognized requirements and specifications, consequently enhancing the overall integrity of the framework or component being produced. Welding examination is not just a procedural step; it is a necessary practice that helps determine potential concerns early, making certain that they are attended to before they rise into considerable issues.
The significance of welding evaluation can be highlighted by its role in keeping safety and security and resilience. Welded joints are typically subjected to extreme problems, and any flaws can compromise the efficiency and durability of the last product. By executing extensive inspection protocols, organizations can make certain compliance with industry guidelines, therefore reducing risks related to structural failings.
Furthermore, reliable welding examination cultivates self-confidence among stakeholders, consisting of clients and regulative bodies, that the task satisfies the finest standards. This not only enhances the reputation of the maker but also contributes to lasting price savings by preventing rework and possible liabilities. Eventually, welding inspection is important to the success and integrity of manufacture jobs, reinforcing the worth of quality control in engineering techniques.
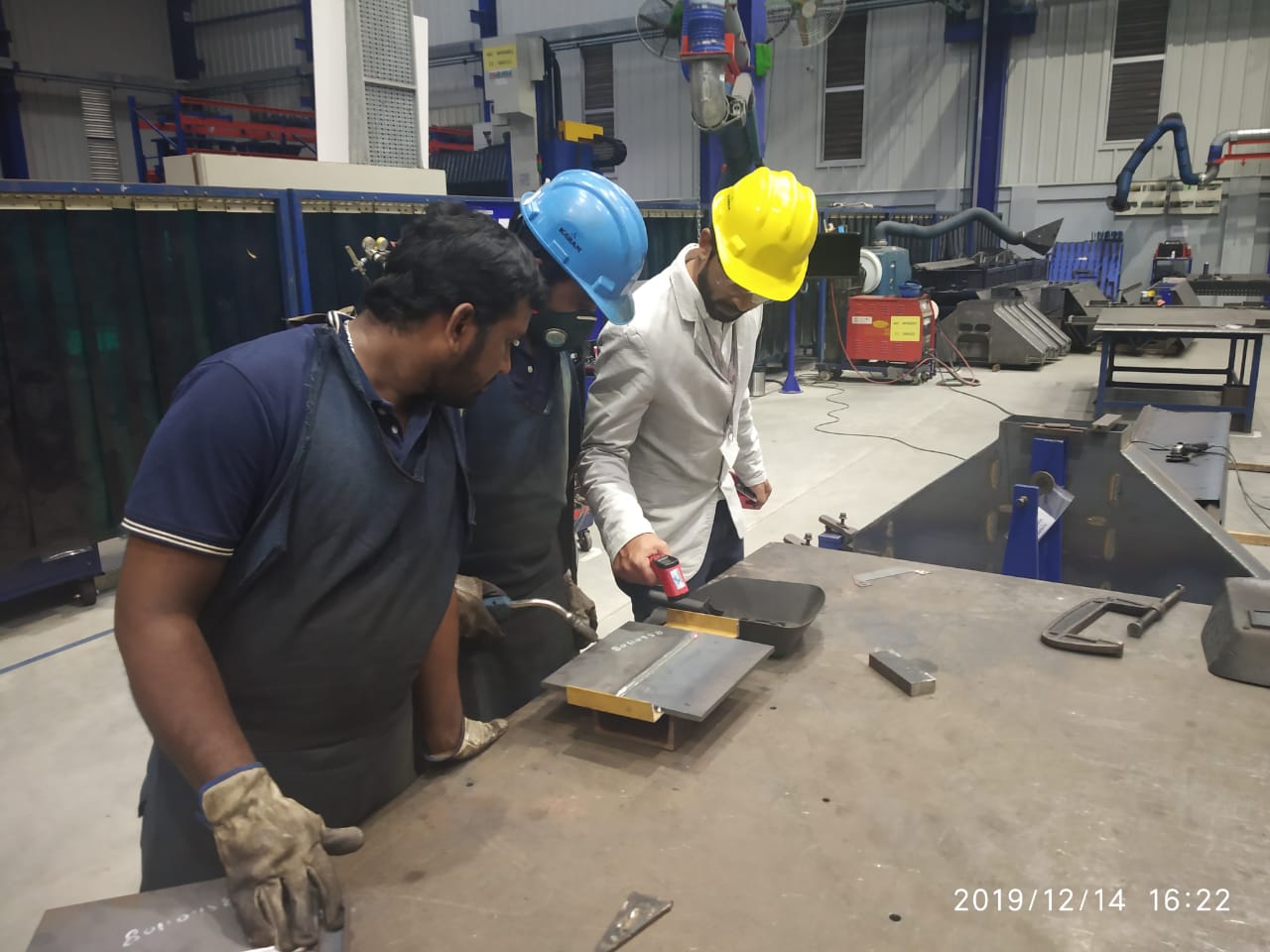
Typical Welding Issues
Welding defects can considerably threaten the architectural integrity of produced components, making their identification and correction vital. Usual welding problems can be broadly classified into 3 kinds: geometric, metallurgical, and service-related.
Geometric issues include issues such as damaging, where the base metal is worn down beside the weld, and excessive convexity, which can result in stress concentration points. These problems can endanger the stamina and durability of the weld joint.
Metallurgical problems develop from improper welding procedures or materials, causing troubles such as porosity, where gas pockets create within the weld, and lack of blend, which takes place when the weld steel stops working to bond effectively with the base metal. These problems can significantly deteriorate the weld's efficiency.
Service-related flaws may not become apparent until after the element remains in use. Examples consist of breaking because of thermal tension or fatigue, which can cause catastrophic failings otherwise dealt with.
Recognizing these common problems equips fabricators to carry out effective inspection strategies that improve the integrity and durability of their projects, ultimately making sure safety and security and performance requirements are met.
Evaluation Methods and Methods
A comprehensive strategy to assessment techniques and approaches is necessary for identifying and alleviating welding flaws in fabrication projects. Numerous techniques are utilized to make sure the stability of welds, consisting of aesthetic inspection, ultrasonic screening (UT), radiographic testing (RT), magnetic fragment screening (MT), and dye penetrant testing (PT) Each technique has its staminas and specific applications.
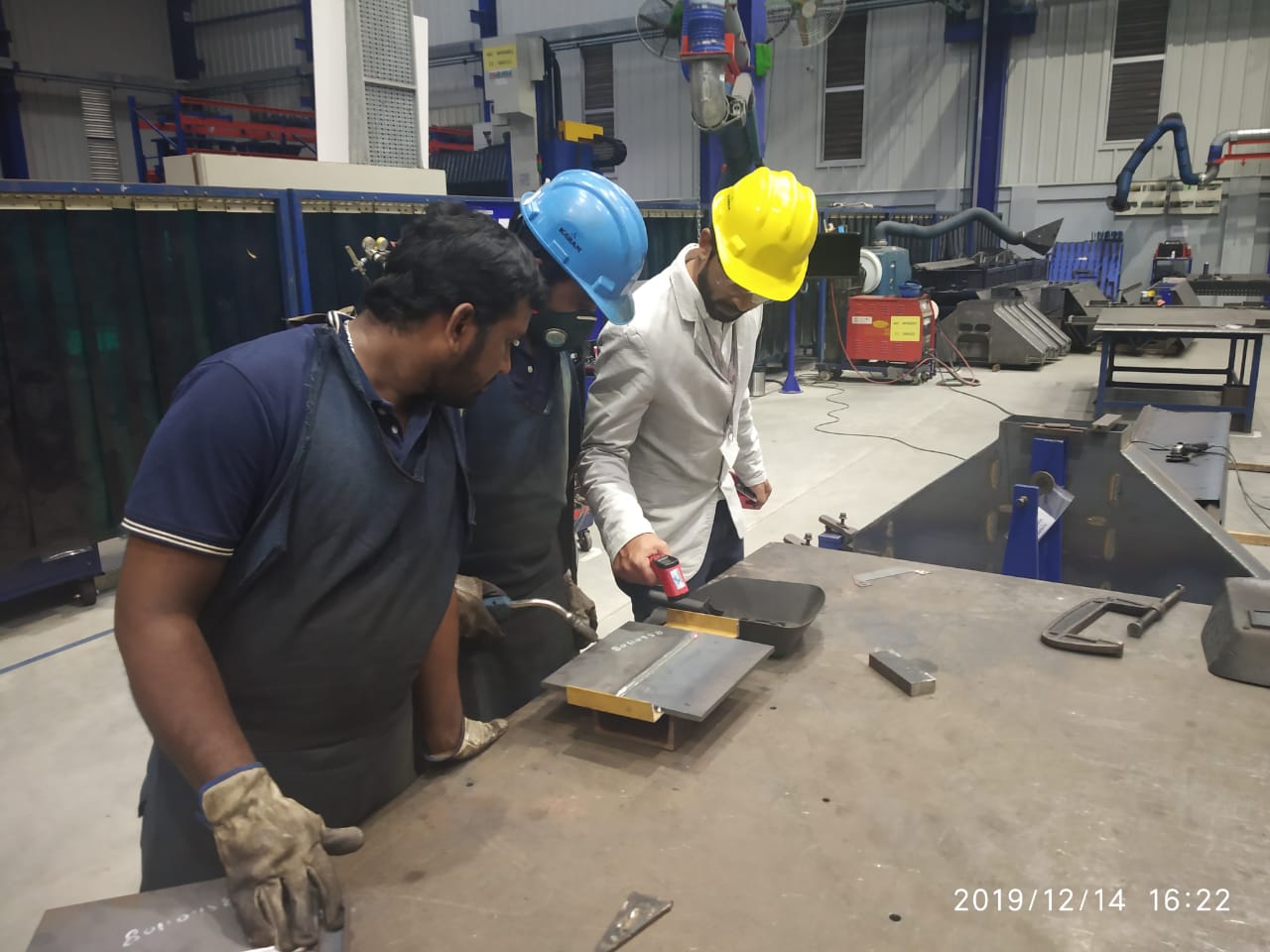
Magnetic fragment screening is helpful for identifying surface and near-surface flaws in ferromagnetic materials. By using a magnetic area and utilizing ferrous particles, assessors can recognize suspensions efficiently. Lastly, color penetrant screening highlights surface-breaking flaws with the application of a dye that leaks right into fractures, making them visible check my source under ultraviolet light.
Employing a combination of these methods ensures an extensive evaluation, boosting the dependability of welded structures.
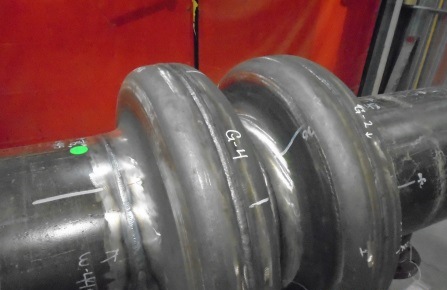
Influence On Task Durability
Efficient assessment methods considerably affect the durability of manufacture tasks. By identifying prospective defects and disparities in welding procedures, evaluations ensure that frameworks are constructed to hold up against functional anxieties gradually. When welds are completely checked out, the probability of unseen concerns, which could cause architectural failings, is lessened.
Routine examinations help with adherence to market criteria and guidelines, which are vital for making sure the sturdiness of bonded joints. Such conformity not just enhances the honesty of the project but also comforts stakeholders pertaining to the quality of the my response job. Additionally, timely detection of defects permits corrective actions to be taken early, stopping costly repair services or full overhauls down the line.
Additionally, reliable assessment methods cultivate a society of quality guarantee within fabrication teams. They are more likely to adhere to ideal techniques and keep high standards throughout the manufacturing procedure when workers are mindful that their job will certainly be rigorously assessed. Eventually, this dedication to high quality not only expands the life-span of the task however also decreases maintenance prices, consequently enhancing the overall economic stability of construction ventures.
Enhancing Reliability in Construction
Reliability in construction is considerably enhanced via extensive examination procedures that resolve possible weaknesses in welding methods. Effective welding evaluation not just determines problems early yet additionally supplies critical responses to welders, guaranteeing adherence to established specifications and standards. By utilizing non-destructive screening approaches, such as radiographic or ultrasonic evaluations, makers can establish the stability of welds without endangering the material.
In addition, regular assessments cultivate a society of high quality and responsibility among manufacture groups. They are a lot more likely to stick to best protocols and methods when welders understand that their job is subject to stringent evaluations. This proactive method minimizes the risk of pricey failures during the operational phase of a job.
Eventually, boosting dependability in construction through detailed examination processes not only boosts the lifespan of the made components but likewise strengthens stakeholder confidence in find here the task's general high quality and sturdiness. Spending in durable welding examination techniques is important for accomplishing long-term reliability in any kind of manufacture venture.
Final Thought
In summary, welding examination works as a crucial part in making sure the long life and dependability of fabrication tasks. By determining problems early and using non-destructive screening techniques, evaluations promote a society of top quality guarantee that abides by industry requirements. The systematic documentation of results not just promotes fad analysis yet also enhances accountability and architectural stability. Eventually, reliable welding inspection methods strengthen stakeholder self-confidence and dramatically add to the financial viability of manufacture undertakings.
Welding examination offers as a fundamental component in guaranteeing the durability and integrity of construction jobs.Guaranteeing high quality with welding evaluation is a vital element of any kind of fabrication task. Ultimately, welding evaluation is essential to the success and integrity of manufacture tasks, strengthening the worth of quality assurance in engineering practices.
An extensive approach to evaluation methods and methods is crucial for identifying and minimizing welding defects in manufacture tasks.In summary, welding evaluation offers as a crucial component in ensuring the durability and reliability of fabrication tasks.
Report this page